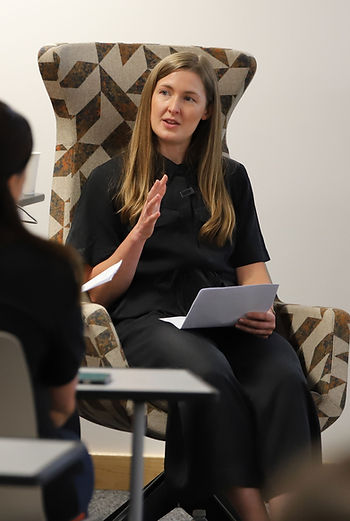
Hannah Sargent of PULSAR® discusses the importance of hi-visibility workwear and the growing relationship between garment durability and safety standards.
For decades, hi-visibility clothing has existed at the heart of employee wellbeing in safety critical work environments. The use of bright colours and reflective materials helps raise wearer visibility and has proven pivotal in protecting working professionals across hazardous fields such as construction, highways, rail and utilities.
Though, whilst the primary purpose of protective clothing is to ensure wearer safety, the ever-changing demands of modern-day work environments continue to stretch the requirements of hi-visibility workwear designs. More than ever before, hi-vis protective clothing must be adaptable and comfortable for both male and female professionals whilst maintaining high levels of reliability in challenging conditions. With that in mind, how are hi-vis garment designs using durability as a way to preserve wearer safety and the environment?
Visibly compliant
By design, hi-visibility workwear is synonymous with fluorescent yellow and orange colours. Such is its importance to user safety; protective clothing is internationally standardised and must comply with EN ISO 20471:2013, with the regulation assessing the suitability and durability of retro-reflective materials and stipulating that ‘high visibility clothing must be capable of visually signalling the user’s presence’.
In many cases, on-site teams are required by law to wear protective workwear and PPE items every day and as a result, employers must provide their staff with the most suitable gear. Hi-visibility clothing must be CE marked and conform to the correct class specification for example, with guidelines ranging from ‘Class 1’ which offers the lowest level of protection to ‘Class 3’ which offers the highest levels of conspicuity. Where end users must take reasonable steps to wear and care for protective equipment, employers are also encouraged to review the condition of hi-vis garments, checking the fluorescent material, reflective strips and contrast material remain at the necessary level of visibility - enabling wearers to stand out in low-light and high-traffic areas.
Although maintenance can help towards preserving the bright colouring of a garment throughout its lifecycle, hi-visibility clothing is habitually exposed to the elements and can become worn and unclean in the process. Occasionally, dirt can simply be wiped clean on outer layers such as jackets, however, next to skin products require regular washes to ensure the item of clothing remains fresh and comfortable for the wearer when in use. With that said, frequent washes can erode the reflective components and fabric of hi-visibility garments, with this process accelerated on poorer quality materials and products. When colour fading, fabric degradation or damage to reflective strips begins to show, a garment may no longer be safe or compliant and will subsequently need replacing.
Careful design, better protection
To combat the signs of wear and reduce the need for replacements, conscious manufacturers and their design teams are actively enhancing the lifecycles of protective clothing at the design stage. Through early collaboration, extensive wearer trials and the sourcing of high-quality, sustainable materials, greater durability is being woven into the plethora of user benefits that hi-vis workwear can offer.
As more significance is placed on the usable service life of hi-vis protective clothing, some high wear workwear garments are now able to retain their colour, fit and quality for up to 50 washes as standard, for example. In many cases, this surpasses the industry standard of 5 washes and allows working professionals to stay visibly safer and more comfortable for longer. Similarly, the adoption of higher-quality materials, finishes and specialised treatments is influencing more practical designs and further reducing the need for repeat replacements. Just as breathable materials can help to regulate wearer temperature, abrasion resistance fabrics and water repellent finishes can support extra protection from the elements and added durability for wearers who may need to kneel for long periods on hard, unforgiving surfaces.
When the reliability of protective clothing does come into question, so too does the safety of the wearer. Therefore, it’s important to replace hi-vis clothing with caution, as low quality replacements may result in another purchase soon after. The approach of buying less has direct benefits to the environment also, whereby end-of-life workwear remains a significant contributor to our planet’s waste, with approximately 90% of the UK’s used workwear and PPE is sent to landfill and incarceration. In fact, it’s understood that by extending the active life of 50% of the UK’s clothing by 9 months, carbon, water and waste footprints can be reduced by 4-10%.
The focus on durability in hi-vis workwear is growing and the need to prioritise multi-functional, reliable and appropriate protective clothing designs is clear. By embracing durability in decision making, employers can protect their workforce and the planet for longer, and all whilst conforming to the latest regulatory standards.